Industrial disc centrifuges have become essential equipment in a variety of sectors, particularly in industries where precision separation is critical. These machines are designed to handle complex mixtures and deliver high-quality output with efficiency and speed. In the dairy, pharmaceutical, and oil industries, the role of disc centrifuges is particularly significant due to the need for reliable and hygienic separation processes. Their ability to manage continuous operations while delivering consistent results makes them a trusted technology in modern industrial production.
Optimizing Dairy Processing with Gentle Efficiency
In the dairy industry, product integrity and hygiene are top priorities. Disc centrifuges are commonly used to separate cream from milk, clarify raw milk, and remove impurities that could affect flavor or shelf life. What makes
disc centrifuge ideal for this sector is their gentle yet effective separation capability. They are engineered to preserve sensitive proteins and fats during high-speed rotation, ensuring that nutritional content and taste remain intact. Modern dairy plants rely on these machines for continuous operation, reducing manual handling and ensuring consistent product quality from batch to batch.
Supporting Pharmaceutical Purity Standards
In pharmaceutical manufacturing, the need for precise, contamination-free separation is non-negotiable. Disc centrifuges play a critical role in processes such as cell harvesting, protein separation, and clarification of fermentation broths. They allow producers to efficiently remove biomass from liquids or isolate valuable compounds with minimal product loss. High-grade materials and sanitary design are key features of pharmaceutical-grade centrifuges. These machines often incorporate fully enclosed systems, clean-in-place capabilities, and compliance with stringent regulatory standards such as GMP. Their use ensures the safety, purity, and effectiveness of pharmaceutical products at every stage of production.
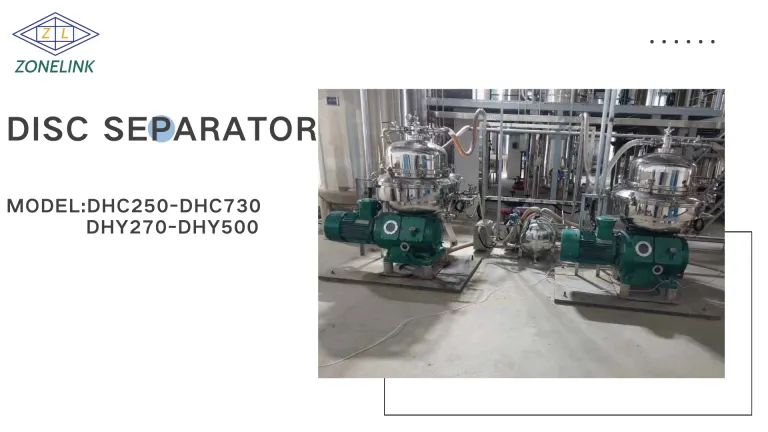
Improving Yield in Oil Refining and Recovery
The oil industry depends on disc centrifuges for the separation of oil from water, solids, and other impurities. Whether processing crude petroleum, edible oils, or lubricants, the goal is to maximize yield while maintaining clarity and quality. Disc centrifuges are particularly useful in separating fine particulates and emulsified water that traditional methods struggle to remove. Their robust construction allows them to handle viscous and abrasive materials over long periods. In edible oil production, they help remove gums and waxes, contributing to clearer and more stable products. In waste oil recovery, they assist in reclaiming usable oil from sludges, making operations more sustainable and cost-efficient.
Adaptability Across Process Requirements
One of the greatest strengths of industrial disc centrifuges is their adaptability. Each industry has unique requirements in terms of flow rates, temperatures, product sensitivity, and cleanliness. Manufacturers offer machines with customizable features such as different disc stack configurations, variable bowl speeds, and automated discharge systems. This flexibility allows centrifuges to be precisely tuned for a particular process, ensuring optimal separation performance regardless of the application. Whether handling delicate dairy products or harsh chemical slurries, disc centrifuges can be configured to meet exact operational needs.
Automation and Smart Integration for Modern Facilities
As industries evolve, the need for automated, data-driven equipment has become more prominent. Disc centrifuges today are often integrated with advanced control systems that monitor performance in real time. Automated settings for bowl rotation speed, product flow, and sludge discharge enhance productivity while reducing human error. These smart systems not only simplify operation but also support predictive maintenance by alerting operators to potential issues before they escalate. In highly regulated environments like pharmaceutical production, such automation helps ensure compliance and traceability.
Energy Efficiency and Environmental Considerations
Modern disc centrifuges are designed with energy efficiency in mind. By optimizing motor design, improving material flow paths, and reducing friction, these machines consume less power while maintaining high performance. Their ability to reduce the need for disposable filters and chemical additives also contributes to lower environmental impact. In wastewater treatment or oil recovery, for example, they help minimize waste and enable resource recycling. This focus on sustainability makes disc centrifuges an attractive option for industries seeking to align with global environmental standards and reduce operational costs.
Reliable Operation for Long-Term Productivity
Industrial disc centrifuges are built for continuous, heavy-duty use. Their durable construction and reliable performance make them a long-term investment in any processing facility. With proper maintenance, these machines can operate efficiently for years, offering consistent results with minimal downtime. Manufacturers also provide robust service support, including spare parts, training, and maintenance planning, to help businesses maximize uptime. Whether in dairy plants, pharmaceutical labs, or oil refineries, disc centrifuges offer a dependable solution for high-volume separation with precision and efficiency.